アルマイト処理と相性が悪い素材形状について
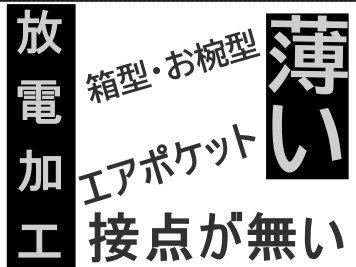
①角・隅部の形状
アルマイト皮膜の約半分は浸透膜厚と呼ばれる層があり、書いて字の如く、アルミの素材を溶解し浸透する事で成膜する層の事です。
例えばピン角と呼ばれるような直角形状の部位にアルマイト処理を行うとピン角先端は殆ど肉が無い為全方向から浸透させた場合十分に浸透させる事が出来ません。
このような場合ピン角の先端はまともに成膜されず、健全な部位に比べ非常に脆くなります。
機械加工を行う時点で完全なピン角は基本的にありませんが、糸面取り等、面取り形状が小さい場合も結局角が出来てしまう為、角部の形状はR形状が最も良好な形状と言えます。
隅部についても同様で直角の隅部(エンドミル加工では不可能ですが)はピン角同様半端な皮膜となり健全な皮膜は得られません。
- 角形状について(クリックで拡大表示)
- 隅形状について(クリックで拡大表示)
②箱型・お椀型製品
アルマイト処理を行う為には皮膜が欲しい面は必ず電解液と接触させる必要があります。
コップ形状や箱形状の場合内部に空気が溜まってしまう為、出来る限りエアポケットが出来ないような姿勢で治具へ取付けを行いますが、内部形状が複雑な場合内部の隅部に予期しないエアポケット(空気溜り)が出来てしまう事や電解液が上手く循環できず、綺麗なアルマイト皮膜が得られない事があります。
この現象はアルマイト以外の表面処理全般(塗装でもメッキでも)液体に浸漬して皮膜を得る全ての表面処理で問題となります。
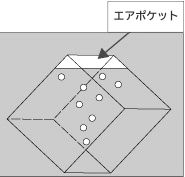
箱型のエアポケット事象例(クリックで拡大)
➂治具へ取り付けに使えそうな形状が無い
アルマイト処理を行う為には製品に電気を供給する為にアルマイト治具にしっかりと固定しなくてはなりません。量産品か1回限りの単品注文かによって最良の治具選択は変わってきますが、確実にワークを固定させるという点だけは共通です。
毎日数千数万個とオーダーがある製品は治具への脱着の工数が重要となります。
年に1回又はリピートが無い製品の場合は脱着工数を基準にする事よりも確実に取り付ける事が重要となります。
単品のオーダーで汎用治具では対応が困難な場合(タップ孔貫通ノック孔が全くない)、支給時にタップ孔やノック孔を追加頂く事も珍しくありません。
アルマイト治具や電極については以下の記事で説明しております。
④極端に薄く長い製品
2mm以上の肉厚があればまず問題はありませんが、薄くて長い製品は特に注意が必要です。
アルマイト皮膜は非常に硬い為、製品が歪むような状態になると皮膜が簡単に割れてしまいます。
薄い板ガラスを歪ませるイメージです。
このように極端に薄くて長い製品には硬質アルマイトは不向きです。
耐摩耗や硬度が必要無い環境で耐食性が目的であれば白アルマイトで十分です。
白アルマイトならば硬度も比較的低く膜厚も薄目なので硬質アルマイトよりも多少割れに強いと言えます。
⑤溶接や放電加工を行った製品
溶接や放電加工・レーザー加工を行った製品にはそのままではアルマイト皮膜が綺麗に乗りません。
放電・レーザー加工を施した製品の加工面には既に酸化膜が出来てしまっている為酸化膜除去の工程を追加し、アルミ全体一皮剥いて綺麗な状態に戻してからアルマイト処理を行う必要があるのですが、そこで問題となるのが、寸法公差です。
酸化膜除去を行う事で製品は多少痩せてしまいますが、厳密に寸法管理までは出来ない為、職人の勘に頼る作業となります。
酸化皮膜剥離については以下の記事で説明しております。
溶接品は溶接部と母材の材質が極端な熱が加わっている為かアルミ合金が変質している為、溶接していない部位と同様の良好な皮膜が得られにくいので外観製品の場合は色も変わってしまい悪目立ちしてしまうでしょう。
しかし、既にアルマイトが施された製品を溶接する事は非常に困難を極めます。